top of page
Call us: 720-470-5510
The Backyard Mechanic
You CAN fix your own car!
We'll teach you how...
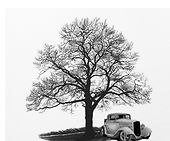
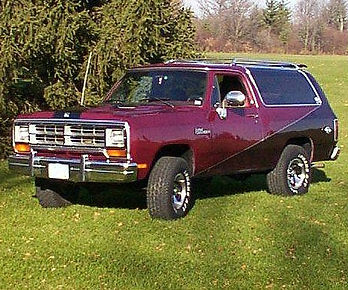
O2 Sensors
Oxygen sensors are an automotive equivalent of the “usual suspects” rounded up by police in the movie classic Casablanca. When the “check engine” or “service engine soon” light appears, it’s usually the O2 sensor that gets the blame.
Sometimes, unfairly.
An oxygen sensor’s job is measuring the proportion of oxygen to unburned fuel in the exhaust and transmitting that information to the engine computer. The O2 sensor is the messenger that tells the computer whether the engine is running rich or lean. The computer uses that data to adjust spark timing and fuel delivery. The computer’s objective is achieving the “stoichiometric ratio,” the ideal mix of fuel and air at which all fuel is burned and no oxygen remains. That’s the ratio that gives maximum economy and lowest emissions.
When the engine computer misses the stoichiometric target by too much and for too long, it sets a diagnostic trouble code and turns on the dreaded warning light.
This doesn’t always mean there is something wrong with the oxygen sensor. Any engine problem which affects fuel delivery or air flow can eventually trigger a trouble code based on O2 sensor data.
For example, a leaking intake manifold gasket will not be spotted by the sensors monitoring air flow into the engine, because that leak is downstream of the sensors. So, the engine computer cannot adjust fuel delivery to compensate for the additional airflow caused by the intake leak. But, that leak will cause excess oxygen in the exhaust and O2 sensor data will trigger the warning light, even though the O2 sensor is not the problem. Similarly, a leaking fuel injector can deliver more fuel than the engine computer intends, causing a rich condition first detected by the O2 sensor. The underlying problem can even be in a different sensor, such as a dirty air flow sensor which underreports the amount of air going into the engine.
Of course, the problem can be the oxygen sensor itself. Oxygen sensors live in the exhaust, which is not a very clean environment. Eventually, an oxygen sensor’s ability to transmit data may deteriorate to the point that it is no longer an effective messenger. That, too, will trigger the warning light.
“Upstream” and “Downstream” O2 Sensor Geography
Oxygen sensor terminology can be confusing. Here’s a guide to deciphering it all.
Oxygen sensors are described as “upstream” or “downstream.” An “upstream” sensor is located near the engine, typically in the exhaust manifold. A “downstream” sensor is located near the catalytic converter. Though both perform the same function – measuring the proportion of unburned fuel and oxygen in the exhaust – the differing data points allow the engine computer to determine whether all of the components in the engine management and emissions systems are properly functioning.
That means, of course, that there will always be at least two O2 sensors in any vehicle – at least those built after 1996, when the emissions regulations requiring oxygen sensors became law.Usually, however, there are more – often as many as four.
Any car with a V engine (V-6, V-8, etc.) will have two upstream sensors, one for each cylinder bank. These are called the “bank 1” and “bank 2” sensors. Bank 1 is whichever cylinder bank has the number one cylinder. That’s the one that fires first in the firing order. (All cylinders on an in-line engine are bank 1.)
The number of downstream sensors varies between manufacturers and vehicles. One will always be located downstream of the catalytic converter, so that there is a measure of the converter’s efficiency. But many car makers use two downstream sensors, one somewhat before of the catalytic converter and the other after it.
Sensors are also described by the number of wires employed: three, four, or five. Because O2 sensors don’t function properly until they reach an operating temperature of about 600ºF., modern practice is to electrically heat the sensor so that it functions as soon as the engine starts. How that is accomplished determines whether three or four wires are used. The latest technology in O2 sensors, the “wideband” sensor, uses five wires. You must replace a sensor with one that uses the same number of wires as the original.
Sensors are either “universal” or “direct fit.” Universal sensors are designed to fit multiple vehicles using the same sensor “bulb,” the part that sticks into the exhaust. But, universal sensors do not come ready to install. The electrical connector will have to be assembled first. In contrast, a direct fit sensor is ready to install right out of the box and simply plugs into the existing wiring.
Which sensor do you replace?
A scan tool or code reader will retrieve the diagnostic trouble code set as the result of an O2 sensor malfunction. Trouble codes are specific to the sensor, so the trouble code will effectively designate the sensor which set the code.
bottom of page